One component that you may not be familiar with is an air injection check valve. Vehicles that use a secondary air injection (AIR) system to reduce tailpipe emissions have one or more of these valves.
Like any automotive part, an AIR check valve can eventually fail—and when it does, you may experience a variety of problems.
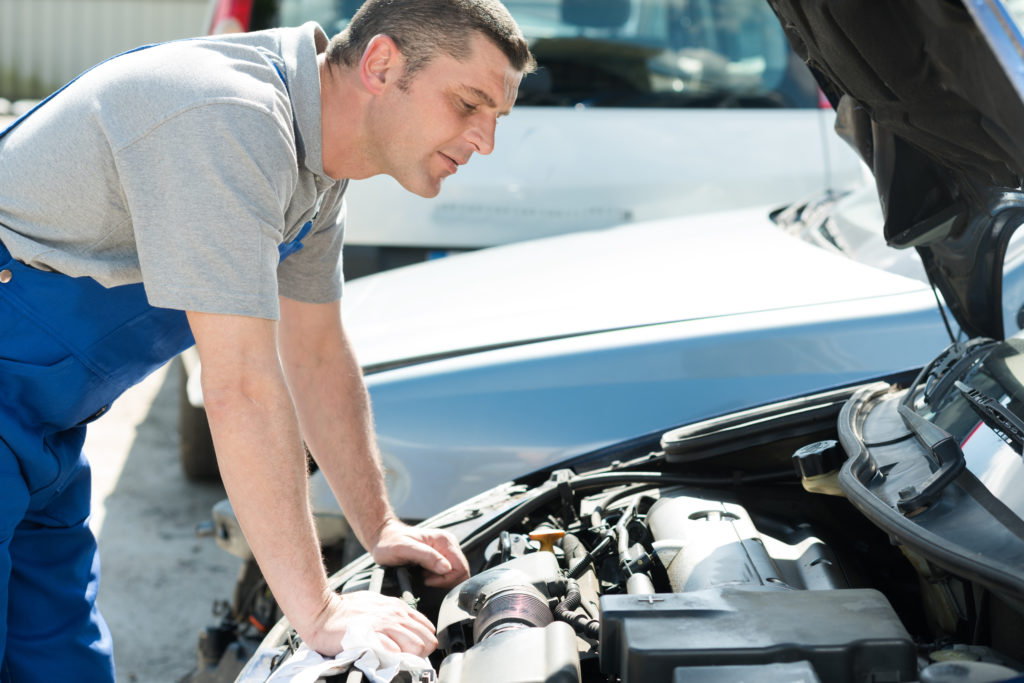
What are the Symptoms of a Bad Air Pump Check Valve?
Not all vehicles have an AIR system—but those that do can experience problems with an AIR check valve (also known as an air inject check valve or an air pump check valve).
Common symptoms of a bad AIR check valve include:
Illuminated Check Engine Light
Your car’s primary computer, which is often referred to as the powertrain control module (PCM), monitors the operation of the AIR system. If the module detects a problem due to a faulty check valve, it will turn on the check engine light and store a diagnostic trouble code (DTC) in its memory.
Common air injection-related DTCs include P0410, P0411, all through P0419.
Increased Tailpipe Emissions
The primary goal of the AIR system is to reduce tailpipe emissions. A faulty AIR check valve can block the flow of air into the exhaust stream, hindering the AIR system’s performance and causing vehicle emissions to increase.
Damage to Other Parts of the AIR System
The AIR check valve prevents reverse exhaust flow from entering the AIR system. If the check valve fails, hot exhaust gases can sneak back into the system, damaging components, such as the air pump and air management valves.
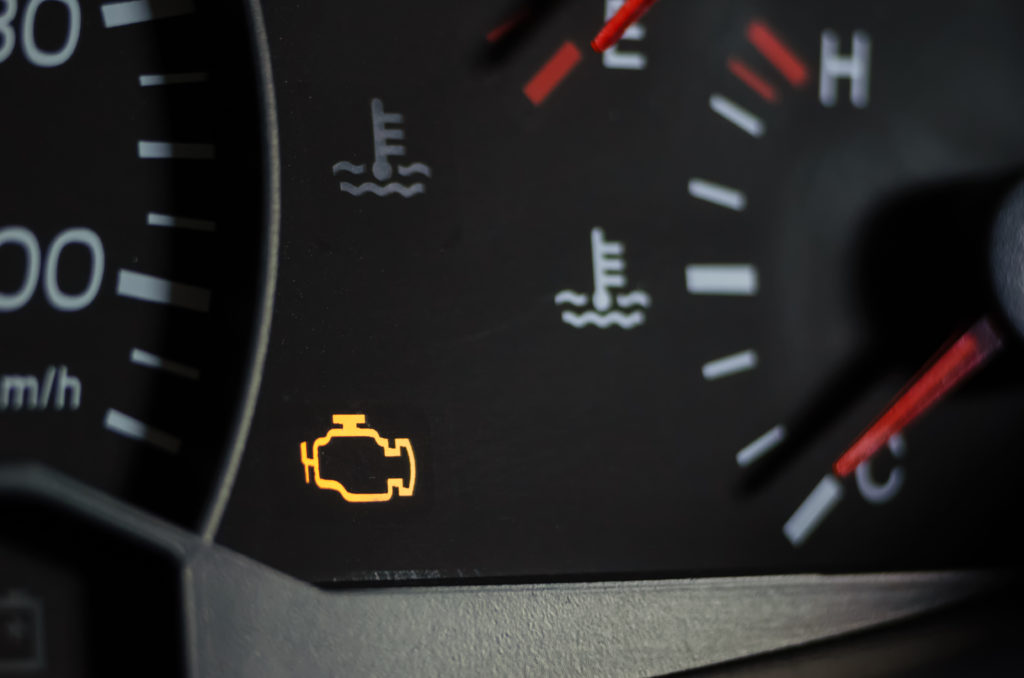
What is an Air Injection Check Valve?
To better understand AIR check valves, it helps to know how the AIR system works. As was mentioned, not all vehicles have an AIR system, but those that do use the technology to reduce tailpipe emissions.
Depending on the vehicle, the AIR system may supply air to the exhaust manifolds, the catalytic converter, or both at different times. The additional air helps reduce harmful exhaust gases through oxidation. Also, the catalytic converter warms up more quickly when air is added to the exhaust manifolds.
The primary components found within a typical AIR system include:
- Air pump (either electric or engine-driven): Supplies air to the AIR system.
- Air management solenoids and valves: Direct air to the check valves and the exhaust manifolds or catalytic converter. There may also be valves that direct air to the atmosphere.
- Check valves: Prevent hot exhaust gases from backing up into the AIR system.
- Necessary plumbing (i.e., hoses and pipes): Connect the various parts of the AIR system.
- Powertrain control module (PCM): Controls the air management solenoids and monitors the operation of the AIR system.

Usually, when the engine is cold, the PCM commands the air management solenoids to direct airflow to the exhaust manifolds. Once the engine warms up, the module commands the solenoids to direct airflow to the catalytic converter.
Note: There are also some systems that direct airflow exclusively to the exhaust manifolds.
As for the check valves, they typically operate in response to airflow and exhaust backpressure. Airflow from the AIR system will cause a check valve to open, whereas extreme exhaust backpressure (from a backfire, etc.) will force a valve to close.
Depending on the system design, there may be just one check valve or multiple check valves. Some check valves are exclusively passive devices, while others are operated by the PCM under certain conditions.
Here is a helpful video that gives an overview of how a typical AIR system works:
Any information provided on this Website is for informational purposes only and is not intended to replace consultation with a professional mechanic. The accuracy and timeliness of the information may change from the time of publication.